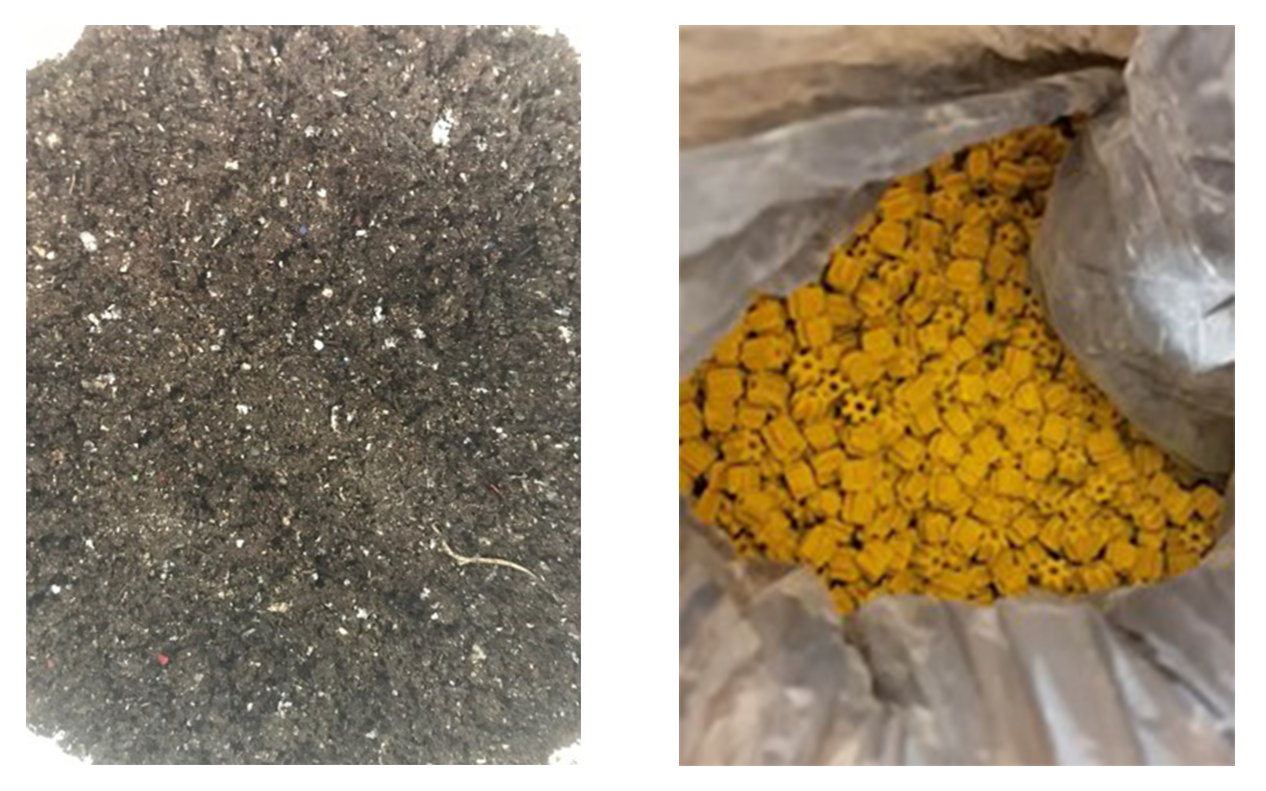
12/02/2025
Optimisation of individual technologies prior to the final flowsheets
An entire work package is dedicated to the optimisation of the flexible technologies within the electrochemical toolbox. This step is a key to the next phases of the development of the final FIREFLY recycling process, which is planned to establish its final flowsheet within the next months.
Mechanochemical processing (MCP): Working with spent DeNOx catalysts, researchers at KUL have already achieved their target, by recovering over 95 % W and more than 80 % V. Promising recovery rate of Pd (~100%) was also reported for Pd-based catalysts which have been used in the lignin depolymerization process. During the next months, the optimisation of the MCP process will be extended to the Pd-catalyst based waste streams provided by JM and the V2O5 catalysts.
Electro-driven solvoleaching (ESLX) and Electro-driven solvent extraction (ESX): After reporting 85 % Pd recovery from the spent catalyst and approximately 100 % stripping of Pd in non-aqueous solvent extraction, the flowsheet involving ESLX technology has already been completed and the testing of recycled catalyst in lignin depolymerization process is ongoing. Next months, researchers will prioritise the optimisation of ESX technology.
Electro-leaching (ELX): The operating conditions of the ELX experiments (started at TRL 4) are continuously optimised to improve the leaching extraction yield. Intermediary results reported extraction rates of ≈80 % for V and Mo and ≈25 % W for the samples provided by ENGIE. Treating the spent catalysts delivered by SOLVA, researchers reported recovery rates of ≈65 % for Cu, Mo and Mn, respectively ≈50 % for Ni and Co, and 80 % for V. The ELX does not use H2O2 as oxidating agent; it operates in milder conditions and reduces the chemicals usage. Within the next months, researchers at TEC will continue investigating the ELX process on the samples previously treated by the mechanochemical processing.
Electrochemical Recovery from Molten Salts (ERMS): This technology involves selective chlorination of solid waste material and subsequent electrochemical recovery. The research group at SINTEF have been successfully testing one of their approaches – anodic dissolution of consumables anodes at TRL 4, reporting a successful anodic dissolution of Ti species from spent DeNOx catalyst supplied by ENGIE and V dissolution from synthetic VN. The analysis of the recovered target metals is currently ongoing.
Electrochemical Transformation in Molten Salts (ETMS): The research team has been working on the photoelectrodeposition method for PGMs recovery from the waste streams provided by JM and VITO-SPOT. The previous experimental results have shown a recovery efficiency of 27 % for PGMs. Currently, the team is working on optimizing the recovery by using TiO2 based photocatalysts to aim for 99% of PGM deposition efficiency.
Gas-diffusion electrocrystallisation (GDEx): After achieving 98 % Pd recovery from synthetic solutions, the optimised parameters of GDEx have been applied to the waste streams provided by JM, obtaining over 99 % recovery. However, the researchers still need to address a few technical issues caused by the highly aggressive solvents and the low conductivity of the streams. Next months intensive work will be carried out by VITO’s research team to run new series of experiments with synthetic solutions to test the recovery of Mo, W and V and later applying it to the leachates.
With the individual technologies reaching the last stretch of the optimisation phase, the curiosity rises to benchmark them against state-of-the-art (SoA) technologies. After the summer break of 2025, updated results corroborated with additional analysis will factually indicate the most promising processes that will be integrated in the final flowsheet of the FIREFLY project.
Within a complementary task, researchers at VITO and CLILLE have synthesised, formulated and shaped more than ten (electro)catalysts. The Pd-impregnated catalysts have already been supplied to VITO SPOT team to be tested within lignin depolymerization process.
© La Palma Research Center